
How to Make Kaya Go Board

Kaya Trees from Aya Forestry Bureau
Although Kaya trees grow naturally from the south area of the Kanto region in Japan, there are immense differences in the quality and appearance of Kaya Go Boards depending on the production area. Kaya produced in Hyuga City of Miyazaki prefecture is most highly rated. In addition, Kaya from Aya Forestry Bureau is renowned for its refined grain and is regarded as the most superior quality wood material among all the others. It exudes a unique fragrance, and its elasticity for receiving the stones provides a satisfying UCHIAJI, the feel and sound of placing a stone firmly on the board. It is not an overstatement that most of the Go boards used in the big title games are made of Hyuga Hon-Kaya.
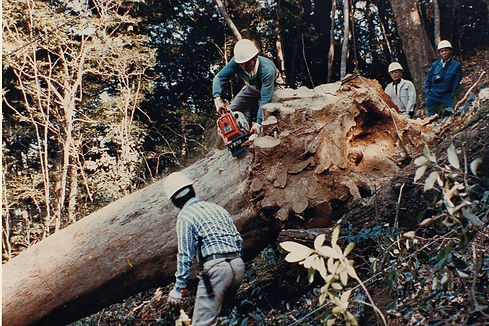
Kaya Tree Logs Collection
Kaya is a precious tree species, so the process of cutting down needs to be extra careful. To avoid splitting and striking when felling down, digging from the root of a Kaya tree is a discreet approach. The price of the Kaya tree in the photo is worth about 20 million JPY at a famous wood market in Japan. However, Japanese national forest has been prohibited from cutting since 2000, leading to a price hike for the Go Boards made of Hon-Kaya from Aya Forestry Bureau because of its increasing rarity.
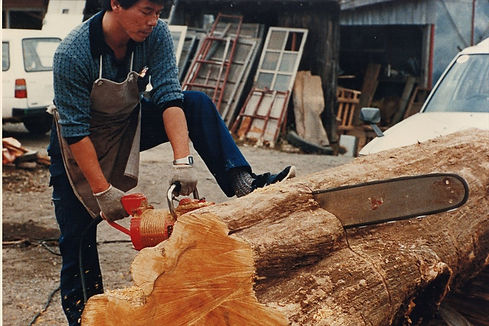
Cutting Go board Out of Log
According to the size and direction of nodes, Kaya logs need to be carefully cut into 54 to 60cm long pieces while avoiding any cracks and defects in order to make more valuable board wood materials. The base of a log has fewer knots, so it suits making Masame and Kiura Go Boards. In comparison, the upper part has more knots, so it becomes the material for Kiomote Go Boards, etc.

Shaping Process of Kaya Go Board
The cut log is then sawed into the shape of a Go board. The basic size is 42.5cm wide x 45.5cm long. But in case the board shrinks, warps, or cracks from the cut surface while drying, the dimension shall be extended 1~1.5cm more in width, 5~8cm more in length as a buffer zone.
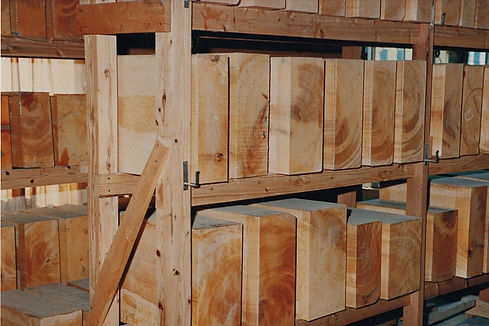
Drying Process of Kaya Wood
After sawing, the boards are treated to prevent splitting and settled to avoid direct sunlight and outdoor air for drying naturally. The length of the drying period is said to be one year per 3cm of its thickness, which means it takes six years for an 18cm thick board to dry out. Regarding the Go boards from our company, Hyuga Go Board & Stone Co., it takes approximately 10 to 15 years for the whole drying process to ensure its complete dryness. If the Go board is not thoroughly dried, it may warp or crack afterward. Therefore this process is time-consuming but extremely crucial.

Traditional Line-making Technique–Tachimori
The thoroughly dried Kaya wood will be made into a Go board by a master, who adopts a traditional Japanese technique, Tachimori, that makes lines on the Go board by using a Japanese sword (Tachi). The master carefully and precisely makes lines one by one with his own hands.
This work, which can be called the final touch of the whole creation, requires an extremely high level of skill and proficiency.
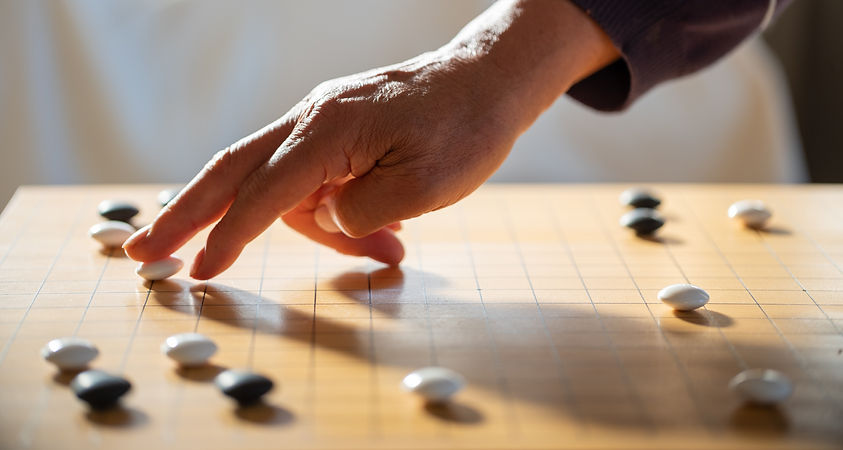